PROZESS-TEMPERATUR SPEZIALISTEN FÜR TEMPERATURKONTROLLE.
VERKAUF. VERMIETEN. SERVICE.
Ihr zuverlässiger Partner für leistungsstarke, energieeffiziente und zuverlässige Prozesskühlung, Heizung und Kühllagerung.
WIR HALTEN INDUSTRIEN AM LAUFEN FÜR …
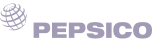

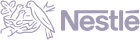

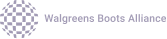

ÜBER UNS
Unser Ziel ist es, industrielle und kritische Prozesse mit effizienten Lösungen zur Temperaturkontrolle durch fachkundige Beratung am Laufen zu halten.
Die Industrie am Laufen halten
Wir tun alles, was nötig ist, um Ihre Branche mit technischen Lösungen am Laufen zu halten. Fachwissen und Notfallunterstützung – 24/7, 365 Tage im Jahr.
Energie-Verbesserungen
Wir helfen Ihnen, Energie zu sparen, Kosten zu senken und Ihren ökologischen Fußabdruck zu verringern – mit unseren eMission Critical Lösungen.
BRAUCHEN SIE NOCH HEUTE EINEN TECHNIKER?
Ganz gleich, ob Sie mit einem Totalausfall Ihres Temperaturkontrollgeräts konfrontiert sind oder dringend technische Unterstützung benötigen, weil Ihr Gerät nicht richtig funktioniert, wir sind nur einen Anruf entfernt.
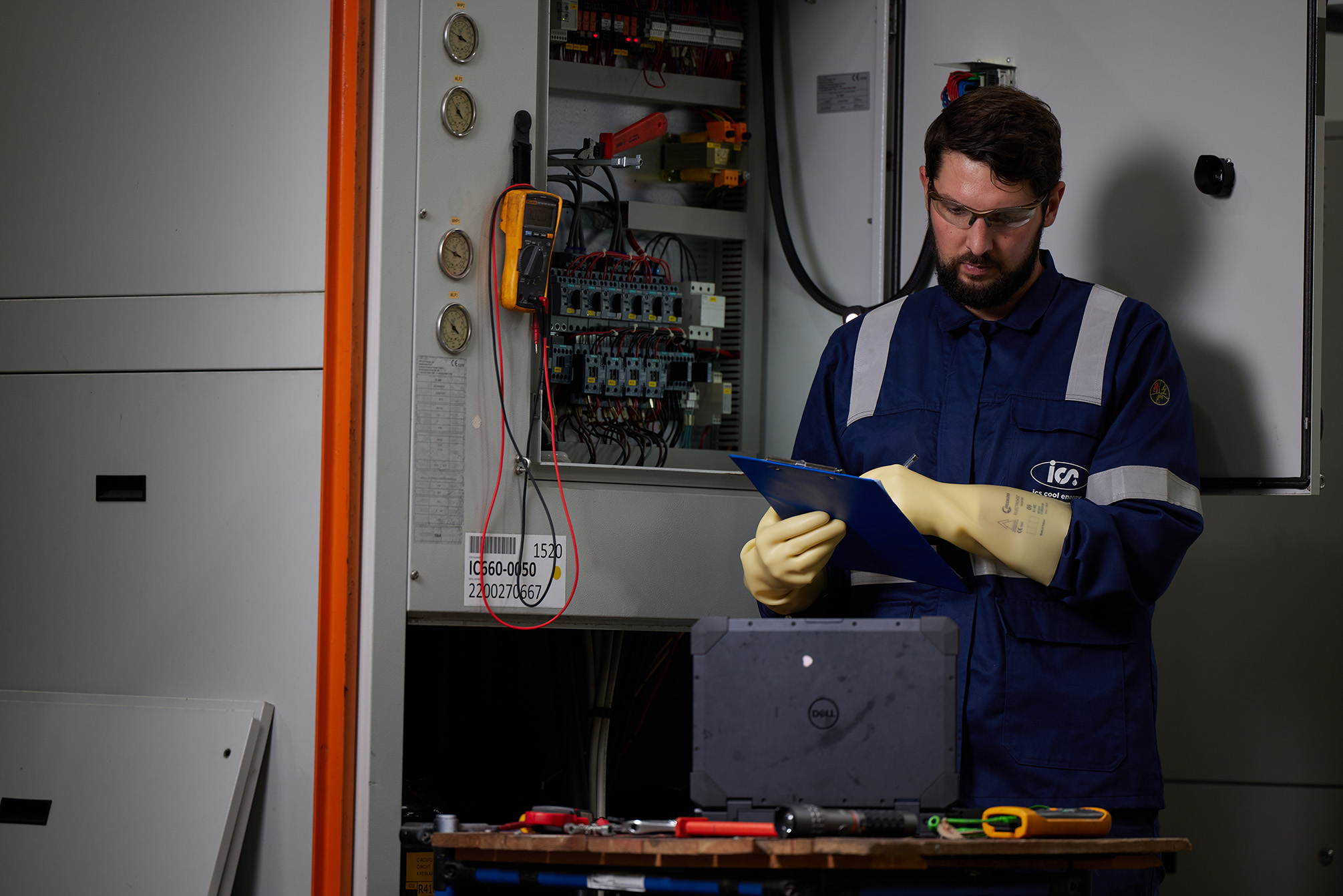
Ausgewählte Fallstudie
[{"id":74284,"link":"https:\/\/www.icscoolenergy.com\/de\/case-studies\/uncategorized\/temperaturregelung-der-automobilindustrie\/","name":"temperaturregelung-der-automobilindustrie","thumbnail":{"url":"https:\/\/www.icscoolenergy.com\/wp-content\/uploads\/sites\/4\/2024\/01\/ICSCE-Plastics-hero.jpg","alt":""},"title":"ICS Cool Energy schlie\u00dft sich mit f\u00fchrendem Hersteller von Automobilkomponenten zusammen","author":{"name":"","link":"https:\/\/www.icscoolenergy.com\/de\/author\/"},"date":"Mai 14, 2019","dateGMT":"2019-05-14 00:00:00","modifiedDate":"2024-01-30 11:43:43","modifiedDateGMT":"2024-01-30 11:43:43","commentCount":"0","commentStatus":"closed","categories":{"coma":"","space":""},"taxonomies":{"applications":"","products":"","topics":"","product_cat":"","translation_priority":"<a href='https:\/\/www.icscoolenergy.com\/de\/?taxonomy=translation_priority&term=optional-de-de' rel='translation_priority'>Optional<\/a>"},"readTime":{"min":1,"sec":8},"status":"publish","excerpt":""},{"id":74000,"link":"https:\/\/www.icscoolenergy.com\/de\/case-studies\/uncategorized\/schnelle-rettung-fuer-temperaturempfindliche-materialien\/","name":"schnelle-rettung-fuer-temperaturempfindliche-materialien","thumbnail":{"url":"https:\/\/www.icscoolenergy.com\/wp-content\/uploads\/sites\/4\/2024\/01\/AirHandlingUnitHire-Square-Ratio.jpg","alt":""},"title":"Schnelle Rettung f\u00fcr temperaturempfindliche Materialien","author":{"name":"","link":"https:\/\/www.icscoolenergy.com\/de\/author\/"},"date":"Aug 16, 2018","dateGMT":"2018-08-16 00:00:00","modifiedDate":"2024-01-30 11:43:43","modifiedDateGMT":"2024-01-30 11:43:43","commentCount":"0","commentStatus":"closed","categories":{"coma":"","space":""},"taxonomies":{"applications":"","products":"","topics":"","product_cat":"","translation_priority":"<a href='https:\/\/www.icscoolenergy.com\/de\/?taxonomy=translation_priority&term=optional-de-de' rel='translation_priority'>Optional<\/a>"},"readTime":{"min":1,"sec":41},"status":"publish","excerpt":""},{"id":73981,"link":"https:\/\/www.icscoolenergy.com\/de\/case-studies\/uncategorized\/gesicherte-forschungsergebnisse-trotz-hitze\/","name":"gesicherte-forschungsergebnisse-trotz-hitze","thumbnail":{"url":"https:\/\/www.icscoolenergy.com\/wp-content\/uploads\/sites\/4\/2024\/01\/Forschung1.jpg","alt":""},"title":"Gesicherte Forschungsergebnisse trotz Hitze","author":{"name":"","link":"https:\/\/www.icscoolenergy.com\/de\/author\/"},"date":"Jul 20, 2018","dateGMT":"2018-07-20 00:00:00","modifiedDate":"2024-01-30 11:43:43","modifiedDateGMT":"2024-01-30 11:43:43","commentCount":"0","commentStatus":"closed","categories":{"coma":"","space":""},"taxonomies":{"applications":"","products":"","topics":"","product_cat":"","translation_priority":"<a href='https:\/\/www.icscoolenergy.com\/de\/?taxonomy=translation_priority&term=optional-de-de' rel='translation_priority'>Optional<\/a>"},"readTime":{"min":1,"sec":35},"status":"publish","excerpt":""},{"id":73772,"link":"https:\/\/www.icscoolenergy.com\/de\/case-studies\/uncategorized\/mobile-kuehltuerme\/","name":"mobile-kuehltuerme","thumbnail":{"url":"https:\/\/www.icscoolenergy.com\/wp-content\/uploads\/sites\/4\/2024\/01\/mobile_kuehltuerme.jpg","alt":""},"title":"Mobile K\u00fchlt\u00fcrme","author":{"name":"","link":"https:\/\/www.icscoolenergy.com\/de\/author\/"},"date":"Nov 8, 2017","dateGMT":"2017-11-08 00:00:00","modifiedDate":"2024-01-30 11:43:50","modifiedDateGMT":"2024-01-30 11:43:50","commentCount":"0","commentStatus":"closed","categories":{"coma":"","space":""},"taxonomies":{"applications":"","products":"","topics":"","product_cat":"","translation_priority":"<a href='https:\/\/www.icscoolenergy.com\/de\/?taxonomy=translation_priority&term=optional-de-de' rel='translation_priority'>Optional<\/a>"},"readTime":{"min":2,"sec":39},"status":"publish","excerpt":""},{"id":73770,"link":"https:\/\/www.icscoolenergy.com\/de\/case-studies\/uncategorized\/10-gruende-fuer-mietkaelte\/","name":"10-gruende-fuer-mietkaelte","thumbnail":{"url":"https:\/\/www.icscoolenergy.com\/wp-content\/uploads\/sites\/4\/2024\/01\/10-gruende-fuer-mietkaelte.png","alt":""},"title":"10 GR\u00dcNDE F\u00dcR MIETK\u00c4LTE","author":{"name":"","link":"https:\/\/www.icscoolenergy.com\/de\/author\/"},"date":"Nov 8, 2017","dateGMT":"2017-11-08 00:00:00","modifiedDate":"2024-01-30 11:43:50","modifiedDateGMT":"2024-01-30 11:43:50","commentCount":"0","commentStatus":"closed","categories":{"coma":"","space":""},"taxonomies":{"applications":"","products":"","topics":"","product_cat":"","translation_priority":"<a href='https:\/\/www.icscoolenergy.com\/de\/?taxonomy=translation_priority&term=optional-de-de' rel='translation_priority'>Optional<\/a>"},"readTime":{"min":3,"sec":8},"status":"publish","excerpt":""},{"id":73764,"link":"https:\/\/www.icscoolenergy.com\/de\/case-studies\/uncategorized\/mietkaelte-fuer-hallenneubau\/","name":"mietkaelte-fuer-hallenneubau","thumbnail":{"url":"https:\/\/www.icscoolenergy.com\/wp-content\/uploads\/sites\/4\/2024\/01\/lebensmittel-branchen.jpg","alt":""},"title":"Mietk\u00e4lte f\u00fcr Hallenneubau","author":{"name":"","link":"https:\/\/www.icscoolenergy.com\/de\/author\/"},"date":"Nov 8, 2017","dateGMT":"2017-11-08 00:00:00","modifiedDate":"2024-01-30 11:43:50","modifiedDateGMT":"2024-01-30 11:43:50","commentCount":"0","commentStatus":"closed","categories":{"coma":"","space":""},"taxonomies":{"applications":"","products":"","topics":"","product_cat":"","translation_priority":"<a href='https:\/\/www.icscoolenergy.com\/de\/?taxonomy=translation_priority&term=optional-de-de' rel='translation_priority'>Optional<\/a>"},"readTime":{"min":2,"sec":16},"status":"publish","excerpt":""},{"id":73758,"link":"https:\/\/www.icscoolenergy.com\/de\/case-studies\/uncategorized\/i-chiller-die-naechste-generation-industrieller-kuehlung\/","name":"i-chiller-die-naechste-generation-industrieller-kuehlung","thumbnail":{"url":"https:\/\/www.icscoolenergy.com\/wp-content\/uploads\/sites\/4\/2024\/01\/10-gruende-fuer-mietkaelte.png","alt":""},"title":"I-Chiller - Die n\u00e4chste Generation industrieller K\u00fchlung","author":{"name":"","link":"https:\/\/www.icscoolenergy.com\/de\/author\/"},"date":"Nov 8, 2017","dateGMT":"2017-11-08 00:00:00","modifiedDate":"2024-01-30 11:43:49","modifiedDateGMT":"2024-01-30 11:43:49","commentCount":"0","commentStatus":"closed","categories":{"coma":"","space":""},"taxonomies":{"applications":"","products":"","topics":"","product_cat":"","translation_priority":"<a href='https:\/\/www.icscoolenergy.com\/de\/?taxonomy=translation_priority&term=optional-de-de' rel='translation_priority'>Optional<\/a>"},"readTime":{"min":2,"sec":6},"status":"publish","excerpt":""},{"id":73750,"link":"https:\/\/www.icscoolenergy.com\/de\/case-studies\/uncategorized\/mobile-weinkuehlung-mieten\/","name":"mobile-weinkuehlung-mieten","thumbnail":{"url":"https:\/\/www.icscoolenergy.com\/wp-content\/uploads\/sites\/4\/2024\/01\/Mobile-Weinkuehlung-ICS-Cool-Energy.png","alt":""},"title":"Kontrollierte G\u00e4rf\u00fchrung verbessert Weinqualit\u00e4t","author":{"name":"","link":"https:\/\/www.icscoolenergy.com\/de\/author\/"},"date":"Nov 8, 2017","dateGMT":"2017-11-08 00:00:00","modifiedDate":"2024-01-30 11:43:49","modifiedDateGMT":"2024-01-30 11:43:49","commentCount":"0","commentStatus":"closed","categories":{"coma":"","space":""},"taxonomies":{"applications":"","products":"","topics":"","product_cat":"","translation_priority":"<a href='https:\/\/www.icscoolenergy.com\/de\/?taxonomy=translation_priority&term=optional-de-de' rel='translation_priority'>Optional<\/a>"},"readTime":{"min":3,"sec":57},"status":"publish","excerpt":""},{"id":73744,"link":"https:\/\/www.icscoolenergy.com\/de\/case-studies\/uncategorized\/kuehltuerme-von-ics-cool-energy-fuer-eine-sichere-produktion\/","name":"kuehltuerme-von-ics-cool-energy-fuer-eine-sichere-produktion","thumbnail":{"url":"https:\/\/www.icscoolenergy.com\/wp-content\/uploads\/sites\/4\/2024\/01\/ICS_Cool_Energy_Kuehlturm.jpg","alt":""},"title":"K\u00fchlt\u00fcrme von ICS Cool Energy f\u00fcr eine sichere Produktion","author":{"name":"","link":"https:\/\/www.icscoolenergy.com\/de\/author\/"},"date":"Nov 8, 2017","dateGMT":"2017-11-08 00:00:00","modifiedDate":"2024-01-30 11:43:48","modifiedDateGMT":"2024-01-30 11:43:48","commentCount":"0","commentStatus":"closed","categories":{"coma":"","space":""},"taxonomies":{"applications":"","products":"","topics":"","product_cat":"","translation_priority":"<a href='https:\/\/www.icscoolenergy.com\/de\/?taxonomy=translation_priority&term=optional-de-de' rel='translation_priority'>Optional<\/a>"},"readTime":{"min":2,"sec":51},"status":"publish","excerpt":""},{"id":73738,"link":"https:\/\/www.icscoolenergy.com\/de\/case-studies\/uncategorized\/chemieproduktion-mietkaelte-wird-zur-langzeitloesung\/","name":"chemieproduktion-mietkaelte-wird-zur-langzeitloesung","thumbnail":{"url":"https:\/\/www.icscoolenergy.com\/wp-content\/uploads\/sites\/4\/2024\/01\/teaser-chemie_ics.png","alt":""},"title":"Chemieproduktion: Mietk\u00e4lte wird zur Langzeitl\u00f6sung","author":{"name":"","link":"https:\/\/www.icscoolenergy.com\/de\/author\/"},"date":"Nov 8, 2017","dateGMT":"2017-11-08 00:00:00","modifiedDate":"2024-01-30 11:43:48","modifiedDateGMT":"2024-01-30 11:43:48","commentCount":"0","commentStatus":"closed","categories":{"coma":"","space":""},"taxonomies":{"applications":"","products":"","topics":"","product_cat":"","translation_priority":"<a href='https:\/\/www.icscoolenergy.com\/de\/?taxonomy=translation_priority&term=optional-de-de' rel='translation_priority'>Optional<\/a>"},"readTime":{"min":1,"sec":22},"status":"publish","excerpt":""},{"id":73732,"link":"https:\/\/www.icscoolenergy.com\/de\/case-studies\/uncategorized\/mobile-kaelte-fuers-kuehle-blonde\/","name":"mobile-kaelte-fuers-kuehle-blonde","thumbnail":{"url":"https:\/\/www.icscoolenergy.com\/wp-content\/uploads\/sites\/4\/2024\/01\/Mietkalte_Brauerei.png","alt":""},"title":"Mobile K\u00e4lte f\u00fcrs K\u00fchle Blonde","author":{"name":"","link":"https:\/\/www.icscoolenergy.com\/de\/author\/"},"date":"Nov 8, 2017","dateGMT":"2017-11-08 00:00:00","modifiedDate":"2024-01-30 11:43:48","modifiedDateGMT":"2024-01-30 11:43:48","commentCount":"0","commentStatus":"closed","categories":{"coma":"","space":""},"taxonomies":{"applications":"","products":"","topics":"","product_cat":"","translation_priority":"<a href='https:\/\/www.icscoolenergy.com\/de\/?taxonomy=translation_priority&term=optional-de-de' rel='translation_priority'>Optional<\/a>"},"readTime":{"min":1,"sec":57},"status":"publish","excerpt":""},{"id":73726,"link":"https:\/\/www.icscoolenergy.com\/de\/case-studies\/uncategorized\/supermarktkette-setzt-auf-mietkaelte\/","name":"supermarktkette-setzt-auf-mietkaelte","thumbnail":{"url":"https:\/\/www.icscoolenergy.com\/wp-content\/uploads\/sites\/4\/2024\/01\/198.png","alt":""},"title":"Supermarktkette setzt auf Mietk\u00e4lte","author":{"name":"","link":"https:\/\/www.icscoolenergy.com\/de\/author\/"},"date":"Nov 8, 2017","dateGMT":"2017-11-08 00:00:00","modifiedDate":"2024-01-30 11:43:47","modifiedDateGMT":"2024-01-30 11:43:47","commentCount":"0","commentStatus":"closed","categories":{"coma":"","space":""},"taxonomies":{"applications":"","products":"","topics":"","product_cat":"","translation_priority":"<a href='https:\/\/www.icscoolenergy.com\/de\/?taxonomy=translation_priority&term=optional-de-de' rel='translation_priority'>Optional<\/a>"},"readTime":{"min":3,"sec":29},"status":"publish","excerpt":""}]
[{"id":74284,"link":"https:\/\/www.icscoolenergy.com\/de\/case-studies\/uncategorized\/temperaturregelung-der-automobilindustrie\/","name":"temperaturregelung-der-automobilindustrie","thumbnail":{"url":"https:\/\/www.icscoolenergy.com\/wp-content\/uploads\/sites\/4\/2024\/01\/ICSCE-Plastics-hero.jpg","alt":""},"title":"ICS Cool Energy schlie\u00dft sich mit f\u00fchrendem Hersteller von Automobilkomponenten zusammen","author":{"name":"","link":"https:\/\/www.icscoolenergy.com\/de\/author\/"},"date":"Mai 14, 2019","dateGMT":"2019-05-14 00:00:00","modifiedDate":"2024-01-30 11:43:43","modifiedDateGMT":"2024-01-30 11:43:43","commentCount":"0","commentStatus":"closed","categories":{"coma":"","space":""},"taxonomies":{"applications":"","products":"","topics":"","product_cat":"","translation_priority":"<a href='https:\/\/www.icscoolenergy.com\/de\/?taxonomy=translation_priority&term=optional-de-de' rel='translation_priority'>Optional<\/a>"},"readTime":{"min":1,"sec":8},"status":"publish","excerpt":""},{"id":74000,"link":"https:\/\/www.icscoolenergy.com\/de\/case-studies\/uncategorized\/schnelle-rettung-fuer-temperaturempfindliche-materialien\/","name":"schnelle-rettung-fuer-temperaturempfindliche-materialien","thumbnail":{"url":"https:\/\/www.icscoolenergy.com\/wp-content\/uploads\/sites\/4\/2024\/01\/AirHandlingUnitHire-Square-Ratio.jpg","alt":""},"title":"Schnelle Rettung f\u00fcr temperaturempfindliche Materialien","author":{"name":"","link":"https:\/\/www.icscoolenergy.com\/de\/author\/"},"date":"Aug 16, 2018","dateGMT":"2018-08-16 00:00:00","modifiedDate":"2024-01-30 11:43:43","modifiedDateGMT":"2024-01-30 11:43:43","commentCount":"0","commentStatus":"closed","categories":{"coma":"","space":""},"taxonomies":{"applications":"","products":"","topics":"","product_cat":"","translation_priority":"<a href='https:\/\/www.icscoolenergy.com\/de\/?taxonomy=translation_priority&term=optional-de-de' rel='translation_priority'>Optional<\/a>"},"readTime":{"min":1,"sec":41},"status":"publish","excerpt":""},{"id":73981,"link":"https:\/\/www.icscoolenergy.com\/de\/case-studies\/uncategorized\/gesicherte-forschungsergebnisse-trotz-hitze\/","name":"gesicherte-forschungsergebnisse-trotz-hitze","thumbnail":{"url":"https:\/\/www.icscoolenergy.com\/wp-content\/uploads\/sites\/4\/2024\/01\/Forschung1.jpg","alt":""},"title":"Gesicherte Forschungsergebnisse trotz Hitze","author":{"name":"","link":"https:\/\/www.icscoolenergy.com\/de\/author\/"},"date":"Jul 20, 2018","dateGMT":"2018-07-20 00:00:00","modifiedDate":"2024-01-30 11:43:43","modifiedDateGMT":"2024-01-30 11:43:43","commentCount":"0","commentStatus":"closed","categories":{"coma":"","space":""},"taxonomies":{"applications":"","products":"","topics":"","product_cat":"","translation_priority":"<a href='https:\/\/www.icscoolenergy.com\/de\/?taxonomy=translation_priority&term=optional-de-de' rel='translation_priority'>Optional<\/a>"},"readTime":{"min":1,"sec":35},"status":"publish","excerpt":""},{"id":73772,"link":"https:\/\/www.icscoolenergy.com\/de\/case-studies\/uncategorized\/mobile-kuehltuerme\/","name":"mobile-kuehltuerme","thumbnail":{"url":"https:\/\/www.icscoolenergy.com\/wp-content\/uploads\/sites\/4\/2024\/01\/mobile_kuehltuerme.jpg","alt":""},"title":"Mobile K\u00fchlt\u00fcrme","author":{"name":"","link":"https:\/\/www.icscoolenergy.com\/de\/author\/"},"date":"Nov 8, 2017","dateGMT":"2017-11-08 00:00:00","modifiedDate":"2024-01-30 11:43:50","modifiedDateGMT":"2024-01-30 11:43:50","commentCount":"0","commentStatus":"closed","categories":{"coma":"","space":""},"taxonomies":{"applications":"","products":"","topics":"","product_cat":"","translation_priority":"<a href='https:\/\/www.icscoolenergy.com\/de\/?taxonomy=translation_priority&term=optional-de-de' rel='translation_priority'>Optional<\/a>"},"readTime":{"min":2,"sec":39},"status":"publish","excerpt":""},{"id":73770,"link":"https:\/\/www.icscoolenergy.com\/de\/case-studies\/uncategorized\/10-gruende-fuer-mietkaelte\/","name":"10-gruende-fuer-mietkaelte","thumbnail":{"url":"https:\/\/www.icscoolenergy.com\/wp-content\/uploads\/sites\/4\/2024\/01\/10-gruende-fuer-mietkaelte.png","alt":""},"title":"10 GR\u00dcNDE F\u00dcR MIETK\u00c4LTE","author":{"name":"","link":"https:\/\/www.icscoolenergy.com\/de\/author\/"},"date":"Nov 8, 2017","dateGMT":"2017-11-08 00:00:00","modifiedDate":"2024-01-30 11:43:50","modifiedDateGMT":"2024-01-30 11:43:50","commentCount":"0","commentStatus":"closed","categories":{"coma":"","space":""},"taxonomies":{"applications":"","products":"","topics":"","product_cat":"","translation_priority":"<a href='https:\/\/www.icscoolenergy.com\/de\/?taxonomy=translation_priority&term=optional-de-de' rel='translation_priority'>Optional<\/a>"},"readTime":{"min":3,"sec":8},"status":"publish","excerpt":""},{"id":73764,"link":"https:\/\/www.icscoolenergy.com\/de\/case-studies\/uncategorized\/mietkaelte-fuer-hallenneubau\/","name":"mietkaelte-fuer-hallenneubau","thumbnail":{"url":"https:\/\/www.icscoolenergy.com\/wp-content\/uploads\/sites\/4\/2024\/01\/lebensmittel-branchen.jpg","alt":""},"title":"Mietk\u00e4lte f\u00fcr Hallenneubau","author":{"name":"","link":"https:\/\/www.icscoolenergy.com\/de\/author\/"},"date":"Nov 8, 2017","dateGMT":"2017-11-08 00:00:00","modifiedDate":"2024-01-30 11:43:50","modifiedDateGMT":"2024-01-30 11:43:50","commentCount":"0","commentStatus":"closed","categories":{"coma":"","space":""},"taxonomies":{"applications":"","products":"","topics":"","product_cat":"","translation_priority":"<a href='https:\/\/www.icscoolenergy.com\/de\/?taxonomy=translation_priority&term=optional-de-de' rel='translation_priority'>Optional<\/a>"},"readTime":{"min":2,"sec":16},"status":"publish","excerpt":""},{"id":73758,"link":"https:\/\/www.icscoolenergy.com\/de\/case-studies\/uncategorized\/i-chiller-die-naechste-generation-industrieller-kuehlung\/","name":"i-chiller-die-naechste-generation-industrieller-kuehlung","thumbnail":{"url":"https:\/\/www.icscoolenergy.com\/wp-content\/uploads\/sites\/4\/2024\/01\/10-gruende-fuer-mietkaelte.png","alt":""},"title":"I-Chiller - Die n\u00e4chste Generation industrieller K\u00fchlung","author":{"name":"","link":"https:\/\/www.icscoolenergy.com\/de\/author\/"},"date":"Nov 8, 2017","dateGMT":"2017-11-08 00:00:00","modifiedDate":"2024-01-30 11:43:49","modifiedDateGMT":"2024-01-30 11:43:49","commentCount":"0","commentStatus":"closed","categories":{"coma":"","space":""},"taxonomies":{"applications":"","products":"","topics":"","product_cat":"","translation_priority":"<a href='https:\/\/www.icscoolenergy.com\/de\/?taxonomy=translation_priority&term=optional-de-de' rel='translation_priority'>Optional<\/a>"},"readTime":{"min":2,"sec":6},"status":"publish","excerpt":""},{"id":73750,"link":"https:\/\/www.icscoolenergy.com\/de\/case-studies\/uncategorized\/mobile-weinkuehlung-mieten\/","name":"mobile-weinkuehlung-mieten","thumbnail":{"url":"https:\/\/www.icscoolenergy.com\/wp-content\/uploads\/sites\/4\/2024\/01\/Mobile-Weinkuehlung-ICS-Cool-Energy.png","alt":""},"title":"Kontrollierte G\u00e4rf\u00fchrung verbessert Weinqualit\u00e4t","author":{"name":"","link":"https:\/\/www.icscoolenergy.com\/de\/author\/"},"date":"Nov 8, 2017","dateGMT":"2017-11-08 00:00:00","modifiedDate":"2024-01-30 11:43:49","modifiedDateGMT":"2024-01-30 11:43:49","commentCount":"0","commentStatus":"closed","categories":{"coma":"","space":""},"taxonomies":{"applications":"","products":"","topics":"","product_cat":"","translation_priority":"<a href='https:\/\/www.icscoolenergy.com\/de\/?taxonomy=translation_priority&term=optional-de-de' rel='translation_priority'>Optional<\/a>"},"readTime":{"min":3,"sec":57},"status":"publish","excerpt":""},{"id":73744,"link":"https:\/\/www.icscoolenergy.com\/de\/case-studies\/uncategorized\/kuehltuerme-von-ics-cool-energy-fuer-eine-sichere-produktion\/","name":"kuehltuerme-von-ics-cool-energy-fuer-eine-sichere-produktion","thumbnail":{"url":"https:\/\/www.icscoolenergy.com\/wp-content\/uploads\/sites\/4\/2024\/01\/ICS_Cool_Energy_Kuehlturm.jpg","alt":""},"title":"K\u00fchlt\u00fcrme von ICS Cool Energy f\u00fcr eine sichere Produktion","author":{"name":"","link":"https:\/\/www.icscoolenergy.com\/de\/author\/"},"date":"Nov 8, 2017","dateGMT":"2017-11-08 00:00:00","modifiedDate":"2024-01-30 11:43:48","modifiedDateGMT":"2024-01-30 11:43:48","commentCount":"0","commentStatus":"closed","categories":{"coma":"","space":""},"taxonomies":{"applications":"","products":"","topics":"","product_cat":"","translation_priority":"<a href='https:\/\/www.icscoolenergy.com\/de\/?taxonomy=translation_priority&term=optional-de-de' rel='translation_priority'>Optional<\/a>"},"readTime":{"min":2,"sec":51},"status":"publish","excerpt":""},{"id":73738,"link":"https:\/\/www.icscoolenergy.com\/de\/case-studies\/uncategorized\/chemieproduktion-mietkaelte-wird-zur-langzeitloesung\/","name":"chemieproduktion-mietkaelte-wird-zur-langzeitloesung","thumbnail":{"url":"https:\/\/www.icscoolenergy.com\/wp-content\/uploads\/sites\/4\/2024\/01\/teaser-chemie_ics.png","alt":""},"title":"Chemieproduktion: Mietk\u00e4lte wird zur Langzeitl\u00f6sung","author":{"name":"","link":"https:\/\/www.icscoolenergy.com\/de\/author\/"},"date":"Nov 8, 2017","dateGMT":"2017-11-08 00:00:00","modifiedDate":"2024-01-30 11:43:48","modifiedDateGMT":"2024-01-30 11:43:48","commentCount":"0","commentStatus":"closed","categories":{"coma":"","space":""},"taxonomies":{"applications":"","products":"","topics":"","product_cat":"","translation_priority":"<a href='https:\/\/www.icscoolenergy.com\/de\/?taxonomy=translation_priority&term=optional-de-de' rel='translation_priority'>Optional<\/a>"},"readTime":{"min":1,"sec":22},"status":"publish","excerpt":""},{"id":73732,"link":"https:\/\/www.icscoolenergy.com\/de\/case-studies\/uncategorized\/mobile-kaelte-fuers-kuehle-blonde\/","name":"mobile-kaelte-fuers-kuehle-blonde","thumbnail":{"url":"https:\/\/www.icscoolenergy.com\/wp-content\/uploads\/sites\/4\/2024\/01\/Mietkalte_Brauerei.png","alt":""},"title":"Mobile K\u00e4lte f\u00fcrs K\u00fchle Blonde","author":{"name":"","link":"https:\/\/www.icscoolenergy.com\/de\/author\/"},"date":"Nov 8, 2017","dateGMT":"2017-11-08 00:00:00","modifiedDate":"2024-01-30 11:43:48","modifiedDateGMT":"2024-01-30 11:43:48","commentCount":"0","commentStatus":"closed","categories":{"coma":"","space":""},"taxonomies":{"applications":"","products":"","topics":"","product_cat":"","translation_priority":"<a href='https:\/\/www.icscoolenergy.com\/de\/?taxonomy=translation_priority&term=optional-de-de' rel='translation_priority'>Optional<\/a>"},"readTime":{"min":1,"sec":57},"status":"publish","excerpt":""},{"id":73726,"link":"https:\/\/www.icscoolenergy.com\/de\/case-studies\/uncategorized\/supermarktkette-setzt-auf-mietkaelte\/","name":"supermarktkette-setzt-auf-mietkaelte","thumbnail":{"url":"https:\/\/www.icscoolenergy.com\/wp-content\/uploads\/sites\/4\/2024\/01\/198.png","alt":""},"title":"Supermarktkette setzt auf Mietk\u00e4lte","author":{"name":"","link":"https:\/\/www.icscoolenergy.com\/de\/author\/"},"date":"Nov 8, 2017","dateGMT":"2017-11-08 00:00:00","modifiedDate":"2024-01-30 11:43:47","modifiedDateGMT":"2024-01-30 11:43:47","commentCount":"0","commentStatus":"closed","categories":{"coma":"","space":""},"taxonomies":{"applications":"","products":"","topics":"","product_cat":"","translation_priority":"<a href='https:\/\/www.icscoolenergy.com\/de\/?taxonomy=translation_priority&term=optional-de-de' rel='translation_priority'>Optional<\/a>"},"readTime":{"min":3,"sec":29},"status":"publish","excerpt":""}]
RATGEBER
[{"id":76590,"link":"https:\/\/www.icscoolenergy.com\/de\/nachrichten\/ratgeber\/5-tipps-zur-reduzierung-ihrer-energiekosten\/","name":"5-tipps-zur-reduzierung-ihrer-energiekosten","thumbnail":{"url":"https:\/\/www.icscoolenergy.com\/wp-content\/uploads\/sites\/4\/2024\/01\/5TipsReducedEnergyDACH-1024x536.jpg","alt":""},"title":"Unsere 5 Tipps zur Reduzierung Ihrer Energiekosten","author":{"name":"","link":"https:\/\/www.icscoolenergy.com\/de\/author\/"},"date":"Dez 23, 2020","dateGMT":"2020-12-23 00:00:00","modifiedDate":"2025-04-10 15:25:52","modifiedDateGMT":"2025-04-10 15:25:52","commentCount":"0","commentStatus":"closed","categories":{"coma":"<a href=\"https:\/\/www.icscoolenergy.com\/de\/category\/ratgeber\/\" rel=\"category tag\">Ratgeber<\/a>","space":"<a href=\"https:\/\/www.icscoolenergy.com\/de\/category\/ratgeber\/\" rel=\"category tag\">Ratgeber<\/a>"},"taxonomies":{"post_tag":"","translation_priority":"<a href='https:\/\/www.icscoolenergy.com\/de\/?taxonomy=translation_priority&term=optional-nl' rel='translation_priority'>Optional<\/a>"},"readTime":{"min":2,"sec":7},"status":"publish","content":"Steigende Energiekosten stellen viele Unternehmen vor Herausforderungen \u2013 besonders dort, wo rund um die Uhr"},{"id":76346,"link":"https:\/\/www.icscoolenergy.com\/de\/nachrichten\/ratgeber\/freie-kuehlung\/","name":"freie-kuehlung","thumbnail":{"url":"https:\/\/www.icscoolenergy.com\/wp-content\/uploads\/sites\/4\/2024\/01\/300kW-Freecooler.jpg","alt":""},"title":"Was ist freie K\u00fchlung?","author":{"name":"","link":"https:\/\/www.icscoolenergy.com\/de\/author\/"},"date":"Sep 4, 2020","dateGMT":"2020-09-04 00:00:00","modifiedDate":"2025-04-10 15:07:51","modifiedDateGMT":"2025-04-10 15:07:51","commentCount":"0","commentStatus":"closed","categories":{"coma":"<a href=\"https:\/\/www.icscoolenergy.com\/de\/category\/ratgeber\/\" rel=\"category tag\">Ratgeber<\/a>","space":"<a href=\"https:\/\/www.icscoolenergy.com\/de\/category\/ratgeber\/\" rel=\"category tag\">Ratgeber<\/a>"},"taxonomies":{"post_tag":"","translation_priority":"<a href='https:\/\/www.icscoolenergy.com\/de\/?taxonomy=translation_priority&term=optional-nl' rel='translation_priority'>Optional<\/a>"},"readTime":{"min":3,"sec":36},"status":"publish","content":"Die Anforderungen an moderne K\u00fchlsysteme steigen stetig \u2013 nicht nur hinsichtlich Leistung, sondern auch im"},{"id":76098,"link":"https:\/\/www.icscoolenergy.com\/de\/nachrichten\/ratgeber\/wasseraufbereitung-tipps-fuer-ihren-prozesskuehler\/","name":"wasseraufbereitung-tipps-fuer-ihren-prozesskuehler","thumbnail":{"url":"https:\/\/www.icscoolenergy.com\/wp-content\/uploads\/sites\/4\/2024\/01\/ice-1024x694.jpg","alt":"Water Treatment"},"title":"6 Tipps zur Wasseraufbereitung f\u00fcr Ihren Prozessk\u00fchler","author":{"name":"","link":"https:\/\/www.icscoolenergy.com\/de\/author\/"},"date":"Mai 18, 2020","dateGMT":"2020-05-18 00:00:00","modifiedDate":"2025-04-10 15:35:02","modifiedDateGMT":"2025-04-10 15:35:02","commentCount":"0","commentStatus":"closed","categories":{"coma":"<a href=\"https:\/\/www.icscoolenergy.com\/de\/category\/ratgeber\/\" rel=\"category tag\">Ratgeber<\/a>","space":"<a href=\"https:\/\/www.icscoolenergy.com\/de\/category\/ratgeber\/\" rel=\"category tag\">Ratgeber<\/a>"},"taxonomies":{"post_tag":"","translation_priority":"<a href='https:\/\/www.icscoolenergy.com\/de\/?taxonomy=translation_priority&term=optional-nl' rel='translation_priority'>Optional<\/a>"},"readTime":{"min":2,"sec":48},"status":"publish","content":"Brent Hall, technischer Manager, bietet seine sechs wichtigsten Tipps zur Verl\u00e4ngerung der Lebensdauer eines K\u00fchlers"}]