Updated: April 3, 2024
51% Reduction In Cooling Running Costs & Flex Membership For Injection Moulding Company
Injection moulding company benefits from equipment, maintenance, and system upgrades with the flexibility of an operating expense.
The Challenge
An injection moulding company, located in Basingstoke and specialising in the manufacturing of products for the automotive industry, recently encountered a critical breakdown of their chiller.
This unexpected challenge not only prompted the need for a reliable and efficient replacement but also presented an opportune moment for the company to upgrade their entire cooling system.
At the same time, the company was also transitioning from a fixed electricity tariff to a flexible pricing structure, which underscored the importance of thoroughly assessing and optimising their energy consumption.
To add to the complexity of the project, the company had an additional objective in mind – to create more space within their plant by relocating the cooling plant outside.
Understanding the unique demands of the situation, the company entrusted us with finding a solution that would address these complexities while delivering a tailored upgrade to their cooling system.
The Solution
In response to the specific needs, we redesigned the manufacturer’s cooling system, installing a brand-new process i-Chiller to power the new primary and secondary circuit system.
The circuits were coupled with a heat exchanger providing crucial separation between the cooling plant and the process side.
This not only allowed to relocate the cooling plant outside, but also meet the manufacturer’s demand to use water on the inside of the system while safeguarding the equipment with glycol on the outside.
To further enhance energy efficiency and boost sustainability, the i-Chiller was paired with an i-FC Freecooler.
Free cooling allows to cool down the process fluid without the intervention of a chiller, whenever the outside temperature is low enough, ensuring reduced energy consumption and lower running costs for the system.
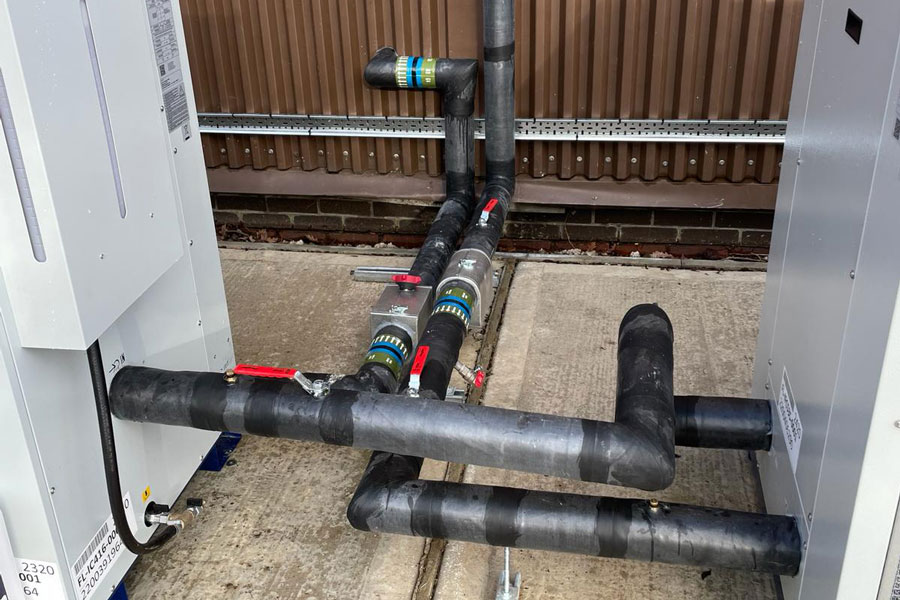
During the inspection and system design, the team also identified specific water quality issues. In response, a side stream filtration system was implemented.
This proactive approach to water treatment is vital for maintaining the chiller’s efficiency and reliability.
Installing the side stream filtration, our service team could ensure the effective removal of solids and prevent particles from entering the system.
Side stream filters have been designed to continuously channel 5-15% of the circulating water through a filter housing resulting in the total system volume being filtered two to three times within a twenty-four-hour period.
Comparing traditional fixed asset purchase option, long-term hire, and the new ICS Cool Energy FLEX Membership option, the injection moulding company decided to cover the project leveraging the FLEX all-inclusive programme.
With FLEX Membership they did not only get access to the latest cutting-edge equipment but also to preventive and 24/7 emergency maintenance, replacements and upgrades for an all-inclusive monthly rate and flexibility of an operating expense.
The Results
The company’s decision to partner with ICS Cool Energy for their cooling system upgrade yielded impressive results across multiple domains. By installing an i-Chiller and an i-FC Freecooler, the company experienced substantial efficiency improvements.
The utilisation of the i-FC Freecooler alone led to a remarkable 51% reduction in cooling system’s running costs, resulting in an annual saving of £9,000 in energy cost.
Furthermore, the adoption of our all-inclusive FLEX Membership enabled the transformation of the company’s process temperature control system from a fixed asset into a dynamic solution.
Aligning with the company’s changing business and process needs, they gained access to new equipment, comprehensive maintenance services, and received the assurance of equipment replacements and upgrades when necessary.
Featured Product Categories
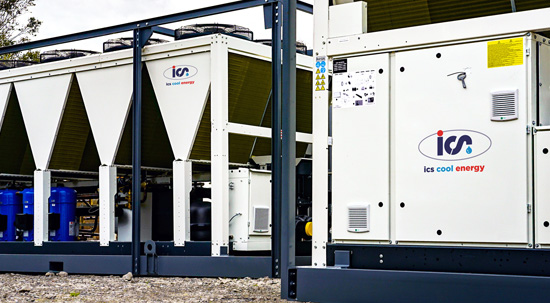
Air cooled chillers
As part of our extensive range of process cooling options, we offer air cooled chillers which are suitable for process cooling and air conditioning applications. With capacities from 17kW to multi-megawatts, these air cooled chillers are capable of cooling processes and buildings of any size and design. Air cooled chillers provide the same function and consist of the exact same design as water cooled chillers, with the main difference being the way heat is transferred into the air as opposed to a water loop. Our range of scroll compressor, air cooled chillers have multiple benefits. These include low footprint, high efficiency, and low noise, ensuring the right product for your application. We've been providing temperature control solutions and service support since 1989, designing turnkey solutions, and working with businesses to create a solution for them, with our standard range in stock for immediately delivery.
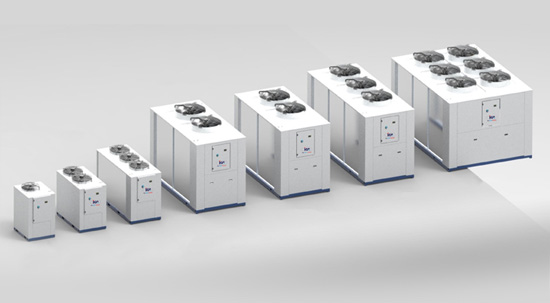
Free cooling chillers
Free Cooling allows businesses to recover up to 80% of their process cooling energy costs by utilising lower ambient temperatures to cool their process application and reducing the need to power the chiller. Available as independent units or integrated with your process chiller, free coolers can be retrofitted into your existing process or installed as part of a turnkey solution. Working with businesses in the manufacturing and facilities management industries, we have lowered their energy costs and reduced their environmental impact through free cooling systems. Given the intrinsically process-heavy nature of the UK’s industrial manufacturing, process cooling is one of the biggest costs incurred. For many industrial end-users, process cooling is achieved solely via an air or water-cooled chiller or cooling tower. However, all industrial applications with a water leaving temperature of 10°C or more – regardless of sector – can start to be cooled via the external ambient air temperature, rather than by electro-mechanical refrigeration, thanks to a process known as free cooling. <strong>Up to 80% energy savings</strong> One of the stand-out benefits of a free cooling system is the sheer amount of energy – and therefore utility bills – it can save. While free cooling can bring about a reduction in energy consumption for any process cooling application with a water leaving temperature of 10°C or more, it should be attractive to larger manufacturers, such as those working in the chemical and pharmaceutical sectors. Further costs can be saved due to the reduced load on the chiller – particularly the compressors and fans – as they are not worked as hard, or at all in some cases. As such, maintenance costs can be lower over the lifetime of the system. From a health and safety point of view, unlike cooling towers, free cooling systems pose no risk of legionella and therefore do not require additional water treatment costs beyond the norm to mitigate the risk of an outbreak.
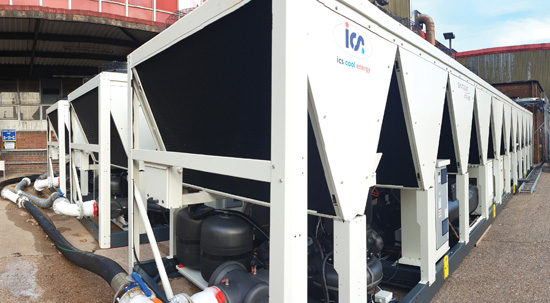
Low GWP chillers
With environmental concerns taking centre stage in the public eye, and the decision making processes in every aspect of business, it is important to be aware of the options available to improve the sustainability of your process. Our range of low global warming potential (GWP) chillers use energy efficient designs and low GWP refrigerants to improve the sustainability of your chillers. With high tariffs being applied to high GWP refrigerants, and rising costs of energy, it also makes financial sense to consider the environmentally friendly options available. We have started the e-Mission critical initiative, dedicated to educating businesses on environmentally friendly solutions to their process and air conditioning requirements, making it the perfect partner for your next temperature control project. <strong>Our energy approach</strong> Since 1989 we have created bespoke temperature control solutions across all manufacturing, industrial, and critical process applications. With a nationwide network of highly experienced technical engineers, we will visit your site to understand your application needs, audit your facilities and potential constraints, and develop the optimum solution for your individual circumstance. We can design, install, commission, and project manage bespoke turnkey solutions and provide full, tailored, 24/7 maintenance, and breakdown support.
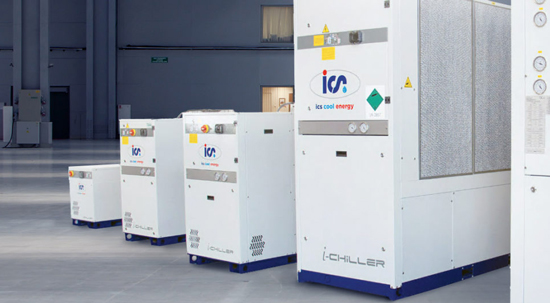
Process chillers
Process chillers are designed and built from the ground up to be more reliable, operate within tighter specified tolerances and to be more robust for continued operation when compared to chillers designed for HVAC. Our i-Chillers are specifically designed to cope with the rigours of manufacturing and critical processes. Process chillers may cost slightly more than equivalent HVAC or comfort chillers but are significantly better value and fit for purpose in a critical process. A process chiller will deliver more accurate leaving water temperature, operate trouble free for longer, have a lower op-ex cost and a greater residual value. <strong>Chillers built for process</strong> Our range of process chillers is designed specifically for process, with features such as unique finned coil evaporators immersed inside the cold-water tank, making them less susceptible to freezing and able to cope with variable load and process fluctuations. The large integrated cold side buffer tank enables closer temperature control for process tolerance and reduces wear and tear from compressor start and stop operations. i-Chillers have high-pressure pumps as standard to cope with the more complex pipework found in process applications. Being fully enclosed in robust steel panels not only protects but creates a smaller footprint for ease of access and plug & play installation. <strong>Our approach</strong> Since 1989 we have created bespoke temperature control solutions across all manufacturing, industrial and critical process applications. With a network of highly experienced technical engineers nationwide, we will visit your site to understand your exact application needs and audit your facilities and potential constraints to develop the optimum solution for your circumstances. We can design, install, commission and project manage bespoke turnkey solutions and provide full, tailored 24/7 maintenance & breakdown support with our nationwide service & hire team.